cement industry finish grinding process
2023-03-27T15:03:47+00:00
116 Portland Cement Manufacturing US EPA
Aug 17, 1971 to the process during the finish grinding operations described below [5] Figure 1, which depicts life cycle steps in the production of cement, includes Princeton’s NetZero America study Annex K: Cement Feb 6, 2020 Cement grinding (3060 kWh/t of clinker) Where the above numbers Cement Finish Milling (Part 2: Comminution) LinkedIn
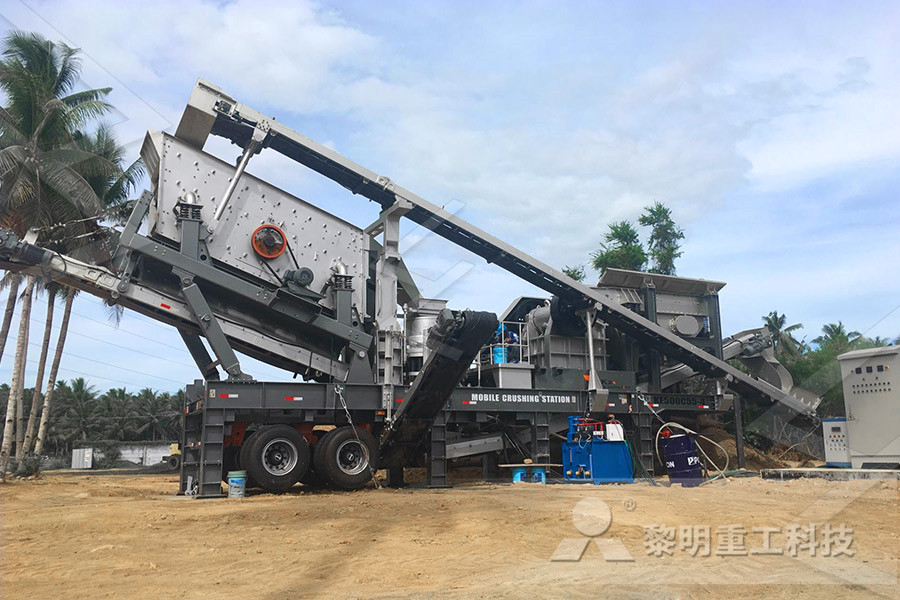
Cement Manufacturing Process Phases Flow Chart
Aug 30, 2012 Final process of 5 th phase is the final grinding There is a horizontal filled with steel balls Clinker reach in this rotating drum after cooling Here, steel balls tumble and crush the clinker into a very fine Cement Industry Baseline Study Process Operations Figure 1 shows a simplified CEMENT INDUSTRY ENERGY BASELINE STUDY Cement Industry Ernst Worrell, Christina Galitsky and Lynn Price vertical shaft kilns Energy Efficiency Improvement Opportunities for the
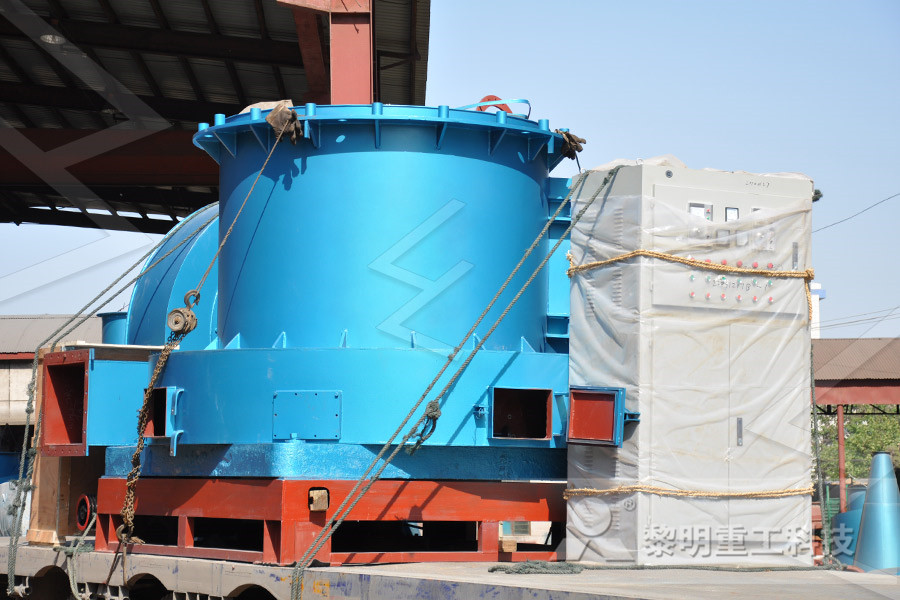
Cement Production Process Cement Manufacturing Process
Aug 25, 2020 In the cement grinding process, the clinker is ground to a fine powder Nov 8, 2012 The cement industry is particularly reliant upon particle size reduction Breakthrough in Clinker Grinding Massachusetts Aug 17, 1971 to the process during the finish grinding operations described below These materials, also excavated from quarries or mines, are generally purchased from an external source, rather than obtained directly from a captive operation by the cement plant The portland cement manufacturing industry is relying116 Portland Cement Manufacturing US EPA
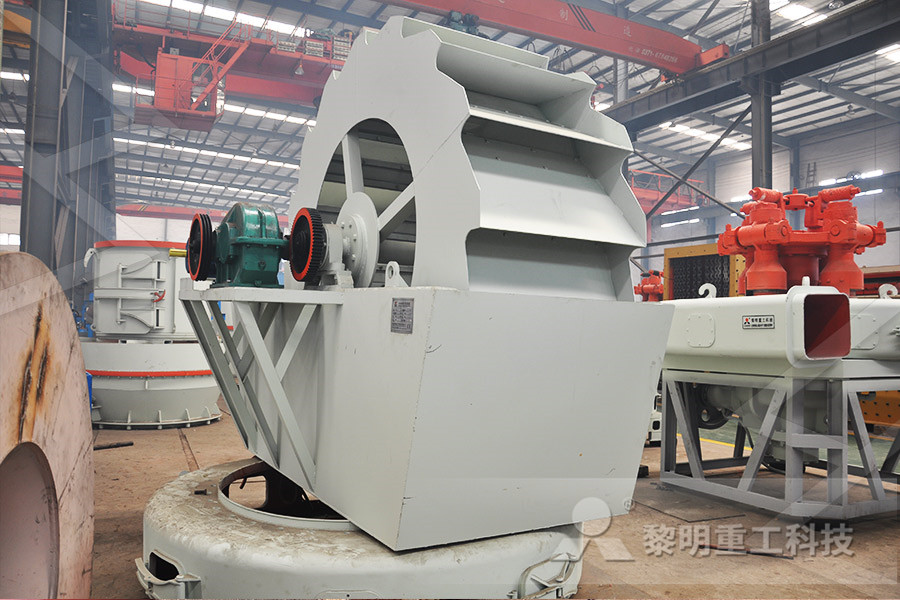
Cement Finish Milling (Part 1: Introduction History) LinkedIn
Dec 2, 2019 The finish mill system in cement manufacturing is the second to last major stage in the process, where the feed material is reduced in size from as large as several centimeters in diameter,Nov 8, 2012 The cement industry is particularly reliant upon particle size reduction Raw materials crushing and grinding seeks to reduce materials from roughly one meter cubes of blasted stone to a size where at least 80 percent of the raw material is less than 75 microns Finish grinding of clinker and other cementBreakthrough in Clinker Grinding Massachusetts Institute Feb 9, 2020 Cement grinding process is the reduction of clinker produced in rotary kilns to a fine form The clinker has to be ground with the addition of gypsum to get the finish product, cement The objective is to A Review on Pyroprocessing Techniques for

Princeton’s NetZero America study Annex K: Cement
The main processes included in the NZAP cement manufacturing model include the grinding of raw materials, high temperature calcination to convert the raw materials to clinker, and a finish grinding process in which additional materials are ground with the clinker to create the fine powder generally referred to as cementJun 13, 2019 Cement Milling / Finish grinding is the last unit operation in the cement manufacturing process (Excluding Cement Packing) However, is most critical not only with regard to powerCement Mills Optimization The Quality Perspective LinkedInIn California, the cement industry employs approximately 1,990 workers and has an annual value of shipments of about $850 million Table 21 presents economic statistics for the California cement industry, as compared to US cement industry totals Table 21 Cement Industry Economic Statistics California US CA share of USINDUSTRIAL CASE STUDY THE EMENT INDUSTRY
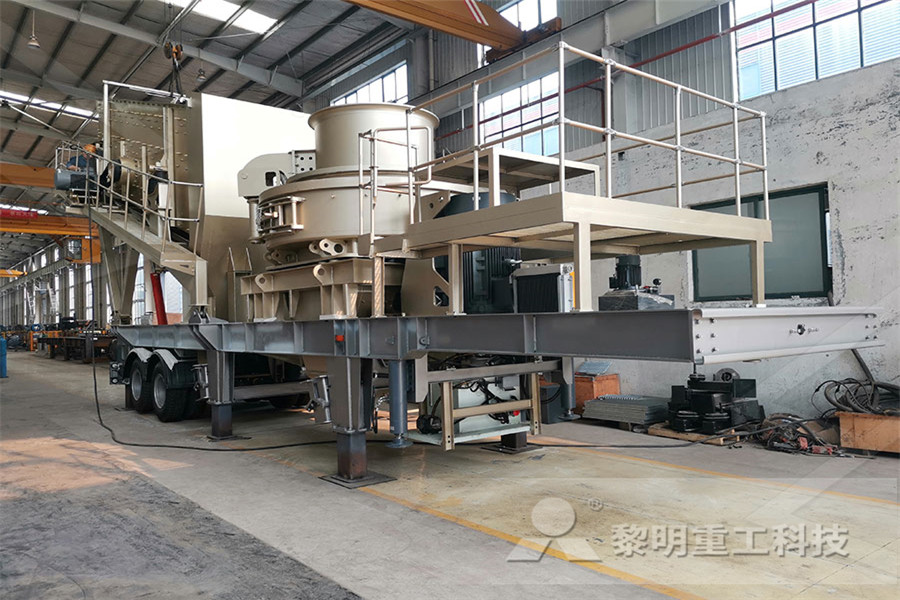
Cement Manufacturing Process: 6 StepsTo Make
Jan 27, 2020 The grinding process is carried out in a closed system, which is equipped with an cement separator to separate cement particles according to size, and materials that are not completely finely ground are Aug 25, 2020 In the cement grinding process, the clinker is ground to a fine powder along with other materials, up to 5% gypsum or additional anhydrite is added to control the solidification time of the cement, and other compounds are added, such as compounds used to regulate fluidity or gas contentCement Production Process Cement Manufacturing Process AGICO CEMENTThe cement industry is the third largest user of coal after the steel and power industries and it consumes more than 5% of total coal produced in India = 410464 (9268%), and finish milling around two third of the used tires end up in the energy recovery process in the cement industry, whereas the rest is used for material recovery Cement Industry an overview ScienceDirect Topics

EnergyEfficient Technologies in Cement Grinding
Oct 5, 2016 Cement is an energyintensive industry in which the grinding circuits use more than 60 % of the total electrical energy consumed and account for most of the manufacturing cost [ 1 ] The requirements for Oct 22, 2016 Cement grinding using Grate Discharge principles developed in the ore milling industry applied to the cement industry This experience plus the years of manufacturing know how unquestionably qualify Grate Discharge grinding for the Cement Industry RAW CEMENT GRINDINGCement Grinding Mineral Processing MetallurgyA raw mill is the equipment used to grind raw materials into "rawmix" during the manufacture of cement Rawmix is then fed to a cement kiln, which transforms it into clinker, which is then ground to make cement in the Rawmill Wikipedia
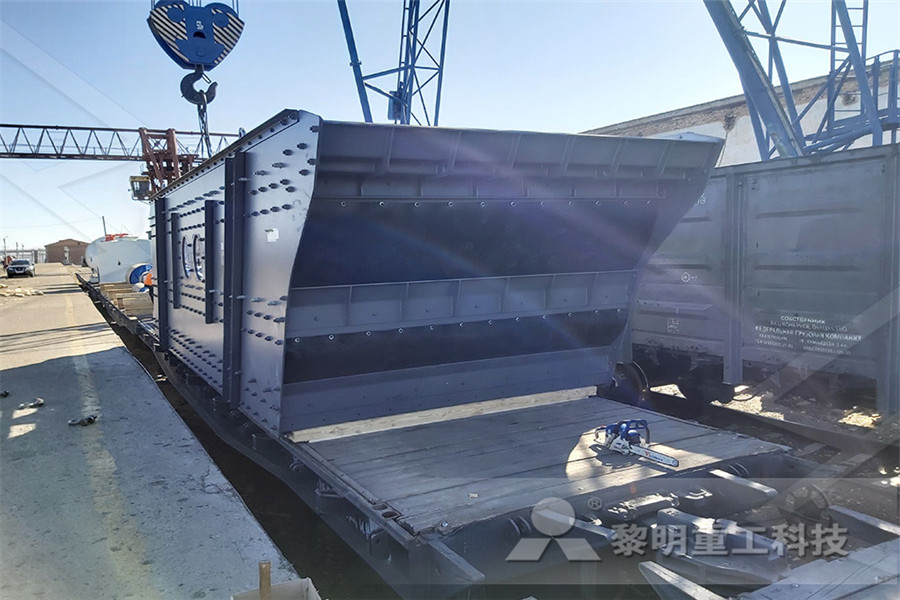
(PDF) Cement Manufacturing ResearchGate
Dec 9, 2015 Show abstract Evaluation of Cement Manufacturing Methods Using Multi Criteria Decision Analysis (MCDA) Conference Paper Dec 2021 Hüseyin Gökçekuş Nivin Ghaboun Dilber Uzun Ozsahin Berna Aug 17, 1971 to the process during the finish grinding operations described below These materials, also excavated from quarries or mines, are generally purchased from an external source, rather than obtained directly from a captive operation by the cement plant The portland cement manufacturing industry is relying116 Portland Cement Manufacturing US EPADec 2, 2019 The finish mill system in cement manufacturing is the second to last major stage in the process, where the feed material is reduced in size from as large as several centimeters in diameter,Cement Finish Milling (Part 1: Introduction History) LinkedIn

Breakthrough in Clinker Grinding Massachusetts Institute
Nov 8, 2012 The cement industry is particularly reliant upon particle size reduction Raw materials crushing and grinding seeks to reduce materials from roughly one meter cubes of blasted stone to a size where at least 80 percent of the raw material is less than 75 microns Finish grinding of clinker and other cementFeb 9, 2020 Pyroprocessing is an important stage in cement manufacturing In this process, materials are subjected to high temperatures so as to cause a chemical or physical change Its control A Review on Pyroprocessing Techniques for The main processes included in the NZAP cement manufacturing model include the grinding of raw materials, high temperature calcination to convert the raw materials to clinker, and a finish grinding process in which additional materials are ground with the clinker to create the fine powder generally referred to as cementPrinceton’s NetZero America study Annex K: Cement

Cement Mills Optimization The Quality Perspective LinkedIn
Jun 13, 2019 Cement Milling / Finish grinding is the last unit operation in the cement manufacturing process (Excluding Cement Packing) However, is most critical not only with regard to powerIn California, the cement industry employs approximately 1,990 workers and has an annual value of shipments of about $850 million Table 21 presents economic statistics for the California cement industry, as compared to US cement industry totals Table 21 Cement Industry Economic Statistics California US CA share of USINDUSTRIAL CASE STUDY THE EMENT INDUSTRYJan 27, 2020 The grinding process is carried out in a closed system, which is equipped with an cement separator to separate cement particles according to size, and materials that are not completely finely ground are Cement Manufacturing Process: 6 StepsTo Make

Cement Industry an overview ScienceDirect Topics
The cement industry is the third largest user of coal after the steel and power industries and it consumes more than 5% of total coal produced in India = 410464 (9268%), and finish milling around two third of the used tires end up in the energy recovery process in the cement industry, whereas the rest is used for material recovery Dec 9, 2015 Evaluation of Cement Manufacturing Methods Using Multi Criteria Decision Analysis (MCDA) Conference Paper Dec 2021 Hüseyin Gökçekuş Nivin Ghaboun Dilber Uzun Ozsahin Berna Uzun View (PDF) Cement Manufacturing ResearchGate• Roller press in semi finish and finish grinding mode • Vertical roller mill (VRM) • Ring roller mill or Horo mill Even though there are various types of systems available for cement grinding, ball mills are predominantly used machines for cement grinding in large number of cement plants In this paper authors are covering the processPROCESS DIAGNOSTIC STUDIES FOR CEMENT MILL

Rawmill Wikipedia
A raw mill is the equipment used to grind raw materials into "rawmix" during the manufacture of cement Rawmix is then fed to a cement kiln, which transforms it into clinker, which is then ground to make cement in the percent of the industry’s total energy 3) Finish Grinding After the clinker is cooled, the clinker nodules are ground into a superfine powder in a horizontal tube containing steel balls During the finish grinding process, the type of cement is determined based upon the type and quantity of additives added CooledCO2 Emissions Profile of the US Cement Industry US EPACHAPTER TWO: CEMENT INDUSTRY 5 21Process Mapping 5 211 Wet Process 7 212 SemiWet Process 8 213 SemiDry Process 8 214 Dry Process 9 215 Finish Grinding Process 15 22 The Cement Manufacturing’s Variables And Factors 23 Summary 18 31 CHAPTER THREE: LEAN MANUFACTURING OVERVIEW 32 31 IMPLEMENTATION OF LEAN WITHIN THE CEMENT